クロムメッキの欠点を補うプラズマコーティング|フィルム搬送性向上
クロムメッキによる離型性・非粘着性の付与
製造現場では、フィルムや粘着テープなどのウェブ搬送工程においてクロムメッキコーティングが広く用いられてきました。クロムメッキ(硬質クロムめっき)は表面を硬く滑らかに仕上げることで、製品の離型性(剥離のしやすさ)や非粘着性が期待できるためです。例えば、粘着剤や樹脂フィルムが接触するロール表面にクロムメッキを施せば、素材がこびり付きにくくなり搬送性が向上します。クロムメッキによるコーティングは耐摩耗性も高く、長年にわたり離型用途で重宝されてきた表面処理技術です。しかしその一方で、クロムメッキには後述するいくつかの欠点や課題が存在し、使用環境によっては十分な効果が得られない場合もあります。ここクロムメッキの課題について詳しく見ていきます。
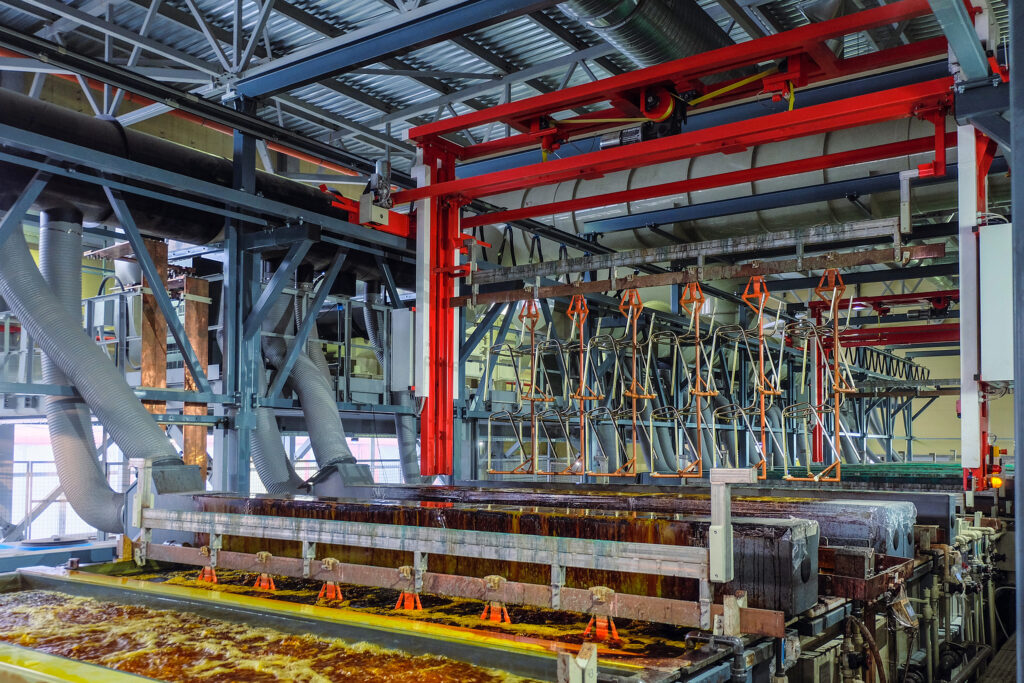
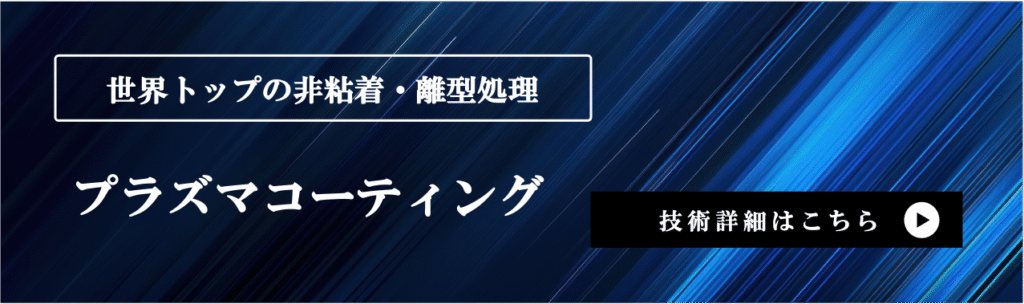
クロムメッキの課題について
腐食環境に対する耐性の限界(酸性環境での溶解しやすさ)
クロムメッキは大気中では安定で錆びにくいとされていますが、実は酸性の環境下では耐食性に限界があります。クロム表面は空気中で形成される酸化被膜により保護されていますが、塩酸などの非酸化性の酸と接するとその被膜が容易に溶解し、金属クロムそのものも腐食・溶解してしまいます。その結果、クロムメッキ皮膜は酸によって短時間で侵され剥離する恐れがあります。特に希薄な塩酸下では硬質クロムめっき皮膜の溶解が促進されることが報告されています。つまり、クロムメッキは一般環境では耐久でも、酸洗浄や酸性ガス雰囲気など腐食性の高い環境では皮膜が劣化・溶解しやすいという弱点があります。
メッキ層の微細なひび割れから始まる劣化
硬質クロムメッキ皮膜には、肉眼では見えない微細なクラック(ひび割れ)が無数に存在します。このマイクロクラックはめっき層内部を貫通し、表面から母材(金属素地)までつながっていることが知られています。そのため、湿度の高い環境や腐食性のガスにさらされると、これら微細なクラックを通じて水分や腐食因子が侵入し、下地の金属に錆(腐食)が発生してしまいます。クロムめっき処理をしているにも関わらず局所的に錆びてしまう原因の一つは、このクラックを起点とした腐食進行にあります。さらに使用中の温度変化や機械的な衝撃によりクラックが拡大・増加すると、皮膜の剥離や劣化が一層進行する恐れがあります。硬質クロムめっきはその特性上どうしても微細ひび割れを伴いますが、この弱点が耐食性や耐久性の面で足かせとなる場合があります。
脱メッキ・再メッキの手間とコスト
クロムメッキ皮膜が劣化・損傷した場合のメンテナンスも大きな課題です。剥がれたり摩耗したメッキ層を修復するには、一度既存のメッキを脱メッキ(化学溶液や電気分解による除去)し、その後改めて再メッキ処理を行う必要があります。一般にこの再メッキ工程は新規にメッキするよりも手間がかかり、費用も高くなる傾向にあります。再メッキには専門設備と有害な薬品(クロム酸や硫酸など)を用いた処理が不可欠で、作業者や環境への負荷も無視できません。実際、標準的な部品であればメッキをやり直すより新品交換する方が安価なケースも多く、再メッキが選択されるのは装置と一体化したロール部品など代替が難しい場合に限られます。さらにメッキ工程そのものに時間がかかるため、生産ラインから部品を外している間のダウンタイムも発生します。このように、クロムメッキ皮膜の補修・更新には手間とコストが掛かる点も大きな欠点と言えるでしょう。
クロムメッキの欠点を補うプラズマコーティング
上記のようなクロムメッキの課題を解決する新たな表面処理技術としておすすめさせていただきたいのが当社のプラズマコーティングです。
プラズマコーティングは、特殊なプラズマプロセスを用いて皮膜を形成する先進コーティング技術です。その最大の特長は、複数の特性を併せ持つ高機能な皮膜を実現できる点にあります。プラズマコーティングの皮膜は、メッキや従来のコーティング処理にはない抜群の非粘着性(離型処理性能)と長寿命を両立しています。この技術によりお客様の使用環境に合わせたオーダーメイドの皮膜特性を付与でき、非粘着性と滑り性(搬送性)の両立など複数の異なる性能を同時に持たせることも可能です。
実際、世界中の紙おむつ製造メーカーやテープ製造メーカー様にて、このプラズマコーティングを非粘着コーティングの標準仕様として採用されています。本技術が離型性や耐久性に優れたグローバルスタンダードになりつつあると自負しております。
プラズマコーティングはクロムメッキの弱点を補う様々なメリットを備えています。
まず非粘着性・離型性において、クロムメッキ以上に優れた効果を発揮します。幅広い種類の樹脂やゴム素材に対しても素材が付着しにくく、清掃の手間を大幅に低減できます。
例えばウェブ搬送ロールの事例では、従来はロール表面に粘着汚れが付着して頻繁な清掃や交換が必要でしたが、プラズマコーティング導入後は2年以上連続使用が可能となり、掃除にかかる手間・人手を著しく削減できたと報告されています。
清掃頻度の低減によって生産ラインの停止時間が減り、結果として工場の稼働コスト低減にも大きく貢献しています。
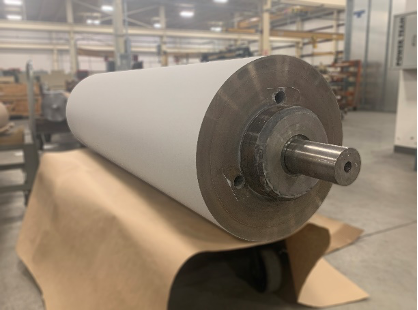
この事例では従来、塗装や特殊テープ貼付といった応急処置で対応していたものの根本解決には至らなかった粘着付着問題が、プラズマコーティングにより解消されています。またこのロールでは、
粘着物が付着しない離型性+フィルムを送るための適度な摩擦(搬送性)という一見相反する特性
が同時に求められましたが、プラズマコーティングはその両立を実現しつつ耐久性も付与できた点が大きな長所でした。
このように、プラズマコーティングは単に表面を非粘着にするだけでなく、耐摩耗性・耐久性を兼ね備えて長期にわたり機能を維持します。さらに皮膜と母材の密着力が高く、衝撃や長期使用による剥離も起きにくいためメンテナンス頻度も低減できます。腐食環境下での耐食性にも優れており、酸・アルカリなどによる腐食に強い耐食皮膜として機能します(耐食性の付与)。
実際にプラズマコーティングは食品機械や医療機器、半導体製造装置、樹脂金型など高い耐食性・非粘着性が要求される分野にも適用が進んでおり、クロムメッキでは対応が難しかった過酷な環境下でも安定した性能を発揮しています。施工プロセスも比較的低温で行われるため、処理時に母材へ与える熱影響が少なく、加工変形や熱によるクラック発生のリスクも抑えられます。さらに、六価クロムなどの有害物質を使用しない処理であることから環境負荷や作業者の安全面にも優れています。以上のように、プラズマコーティングはクロムメッキの欠点を悉く補完し、むしろそれ以上の付加価値を提供できる次世代の表面処理技術として注目されています。
クロムメッキ vs プラズマコーティング
比較項目 | クロムメッキ | プラズマコーティング |
---|---|---|
離型性・非粘着性 | 基本的に離型性は期待できない | 非粘着性に優れ、幅広い樹脂やゴムに対応 |
耐食性 | 微細なひび割れから腐食が進行することがある | 耐食性・環境遮断性が高い仕様もあり |
グリップ力 | 基本的にグリップ力は持たない | 表面の物理的凹凸構造やコーティング材の特性により、高いグリップ力を付与 |
剥がれ・密着性 | 長期使用や衝撃で剥離リスクあり | 基材との高密着により剥がれにくい |
耐久性 | 使用環境によって劣化が早まる可能性あり | 長期間にわたって機能を維持 |
膜厚 | 数μm〜数十μm。電解処理で均一な膜厚管理が可能 | 100μm前後まで形成可能。要望に応じて膜厚調整が可能 |
硬さ | ハードクロムメッキを施工した場合、全ての面が均一的に硬い | 複合皮膜のため、「クロムメッキ相当に硬い材料を含有」程度 |
熱による影響 | 熱による応力でひびや剥がれが生じることがある | 低温処理であり熱の影響が少ない |
メンテナンス性 | 剥がれや劣化で再メッキが必要 | 再施工性が高く、再施工時に母材を傷つけない特殊処理もあり、部分施工も可能 |
環境・安全性 | 六価クロム使用で環境・作業者への影響が懸念 | 有害物質を使用せず、環境・安全性に優れる |
適用分野 | 汎用的に使われているが制限あり | 食品・医療・半導体・樹脂金型など、厳しい要求にも対応 |
コストパフォーマンス | 初期費用はやや安価 | 高い効果と長寿命により、メンテナンスコスト削減に貢献 |
離型性・非粘着性、耐食性、密着性、耐久性、膜厚、熱影響、メンテナンス性、環境安全性、適用分野といった観点で両コーティングの違いをまとめています。
- 離型性・非粘着性
クロムメッキは基本的に離型性は期待できない一方、プラズマコーティングは抜群の非粘着性を持ち、幅広い樹脂・ゴム材料に対して優れた離型性を示します。 - 耐食性
クロムメッキは微細なクラックを起点に腐食が進行することがあり、酸性雰囲気では皮膜が溶解しやすい欠点があります。プラズマコーティングは耐食性・環境遮断性が高い仕様も取り揃えております。 - グリップ力
クロムメッキは基本的にグリップ力を持ちませんが、プラズマコーティングでは表面の物理的凹凸構造と、コーティング材の持つ性能により高いグリップ力を発揮します。 - 密着性(剥がれにくさ)
クロムメッキは長期間の使用や衝撃によって皮膜が剥離するリスクがあります。それに対しプラズマコーティングは下地との密着力が高く、物理的な衝撃や経年による剥がれが起こりにくい特性を持ちます。 - 耐久性
クロムメッキは使用環境(湿度・温度変化・化学物質など)によって劣化が早まる可能性がありますが、プラズマコーティングは高耐久の皮膜構造により長期間にわたり機能を維持します。実稼働環境でも従来比で寿命が飛躍的に向上するケースが報告されています。 - 膜厚
クロムメッキ層の膜厚は一般に数µm〜数十µm程度ですが、プラズマコーティングでは100μm前後まで形成可能です。要望に応じて膜厚調整いたします。ただし、クロムメッキは電解処理で均一な膜厚管理が可能なため、厚みの均質差でいうとクロムメッキが優位となります。 - 熱による影響
クロムメッキは熱応力により皮膜にひび割れが生じたり剥がれたりすることがあります。プラズマコーティングは低温処理であるため加工時の熱歪みが少なく、使用温度変化による皮膜性能劣化も起こりにくくなっています。 - メンテナンス性
クロムメッキは皮膜剥離や摩耗時に再メッキが必要となり、前述の通りメンテナンスの手間・コストが大きいです。一方プラズマコーティングは高い効果・長寿命でメンテナンスコスト削減に寄与します。 - 環境・安全性
クロムメッキ処理には有害な六価クロム化合物を使用するため、廃液処理や作業者への健康影響など環境・安全面の懸念があります。プラズマコーティングは有害物質を一切使用しない皮膜形成法であり、作業環境や製品への安全性に優れています。食品や医療分野でも安心して適用できるクリーンな技術です。 - 適用分野の広さ
クロムメッキは古くから汎用的に使われてきたものの、上記の課題から適用できない条件もありました。プラズマコーティングは離型性・非粘着性と耐久性の両立が求められるウェブ搬送ロールをはじめ、スクリューコンベア、プレート、各種ロール類など様々な部品への施工事例があります。さらに食品製造装置、医療機器、半導体製造装置、樹脂・ゴム金型など厳しい要求条件を伴う分野でも採用が進んでおり、適用範囲の広さでも優位にあります。
以上の比較から明らかなように、プラズマコーティングはクロムメッキの欠点を的確に補うだけでなく、総合的な性能で上回る次世代コーティングと言えます。離型性・非粘着性の付与によるフィルム搬送性の向上はもちろん、耐食性や耐久性、安全性まで兼ね備えているため、現在クロムメッキに代わるソリューションとして注目されています。クロムメッキの課題に直面している現場技術者の方は、プラズマコーティングを一度検討いただく価値があると考えております。
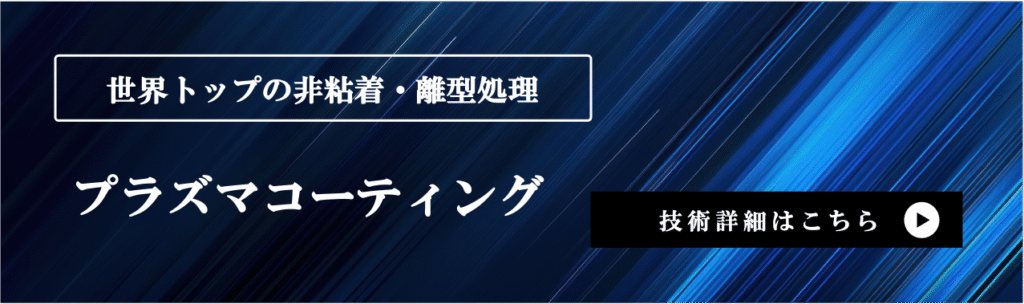