シリコン・テフロンテープに代わる新提案 |テープ製造ラインの改善【大手メーカー事例有】
日々稼働するテープ製造ラインにおいて、粘着剤の付着や部品摩耗にお困りの方もいるでしょう。テフロンテープやシリコンテープで対策をしても、貼り替えの手間やコストが課題となります。また、摩擦による摩耗ですぐに効果が薄れ、根本的な解決に至らないケースも少なくありません。
本記事では、これらのテープに代わる新しい選択肢である「プラズマペーパー」について解説します。大手メーカーの導入事例も紹介するので、製造ラインの課題を解決し、コスト削減と生産性向上を実現したい方は最後までご覧ください。
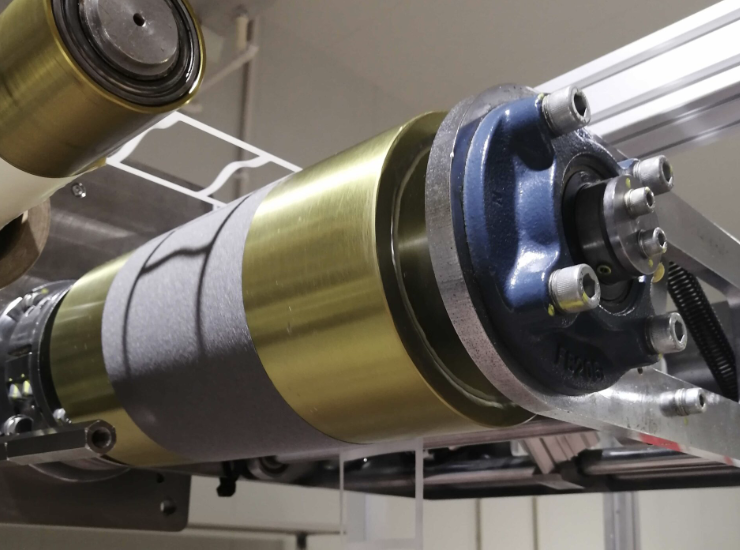
テープ製造ラインにおける主要部品と役割
テープ製造ラインの工程は多岐にわたります。巨大な原反(マスターロール)からテープを巻き出し、製品サイズに裁断・加工し、最終製品として巻き取るまでさまざまな役割を持つ部品が連携して稼働しています。
ラインの中でも代表的な部品と、その役割は以下のとおりです。
部品名称 | 別名 | 用途・工程 |
---|---|---|
テープスリッター | ・スリットマシン・テープ切断機 | ・マスターロールを指定幅に裁断し、多数の小巻に加工する装置。・高速で回転刃が稼働するため、刃やガイド部分の摩耗・粘着剤付着が発生しやすい。 |
テープドロップテーブル&サイド | ・テープ排出テーブル・落下テーブル | ・裁断後のテープを一時的に受け止め、次の工程へスムーズに引き渡す。・テーブル表面に粘着剤やテープの切りくずが残りやすい。 |
トリムガイドドライバー | ・ガイド調整ドライバー・トリミングドライバー | ・テープの端をカットして整え、製品規格に沿った幅に仕上げる。・ガイド部分に糊や粉塵が溜まり、加工精度の低下やライン停止の原因になる。 |
スプライステーブル&洗浄部 | ・塗布台・洗浄ユニット | ・テープ表面に接着剤などの薬剤を塗布したり、異物を洗浄したりする工程。・薬剤の残渣が固着しやすく、安定した品質を保つための維持管理が不可欠。 |
コンベアガイド | ・搬送ガイド・誘導ガイド | ・裁断・加工されたテープを次の工程へ運ぶ際、ズレや蛇行を防ぐためのガイドレール。・テープが常に接触するため、糊や汚れが蓄積しやすい。 |
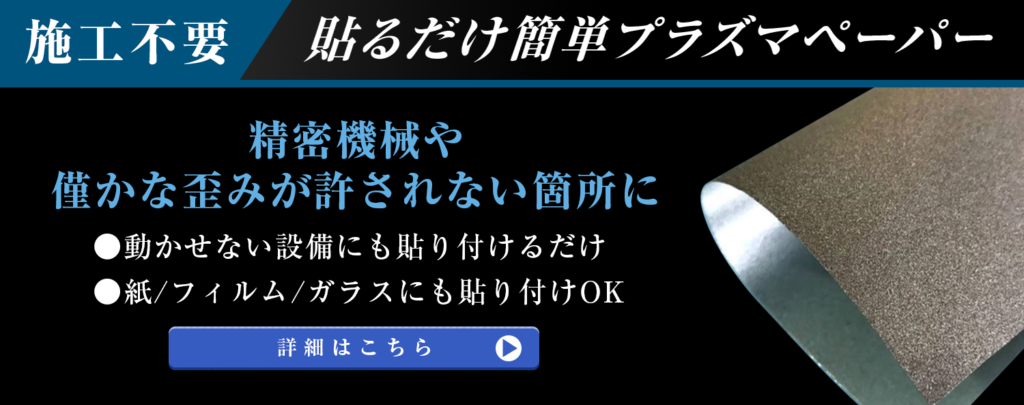
主要部品の課題とシリコン・テフロンテープを用いた対策
テープ製造ラインを安定稼働させるために、各部品のメンテナンスは避けて通れません。ここでは主要部品に共通する課題と対策について、以下の4つの視点で解説します。
- 主要部品に共通していた3つの課題
- シリコンテープの特徴とメリット・デメリット
- テフロンテープの特徴とメリット・デメリット
- シリコンテープ・テフロンテープによる従来の対策
主要部品に共通していた3つの課題
テープ製造ラインの主要部品に共通する3つの課題は以下のとおりです。
- 摩耗による短寿命化
- 粘着剤付着による効率低下
- 交換コストの増大
高速で稼働する部品は常にテープとの摩擦に晒されます。粘着剤と接触し続けるため、表面の劣化や糊残りを避けられません。
例えば、スリッターの刃は摩耗で切れ味が悪くなり、ガイドレールには糊が堆積して製品を傷つけます。これらの部品を交換・清掃するには生産ラインを止める必要があり、人件費や機会損失が大きなコスト負担となっています。
シリコンテープの特徴とメリット・デメリット
これまで課題の対策によく利用されていたのがシリコンテープです。シリコンテープの特徴と、メリット・デメリットについては以下の通りです。
- シリコーン樹脂やシリコーンゴムを基材としており、表面に特有のべたつきがある
- 柔軟性に優れ、ローラーのような曲面や凹凸部にもしっかりフィットする
- 耐熱性・耐寒性に優れており、電気絶縁性が高い
- 屋外での使用にも耐える耐候性を持つ
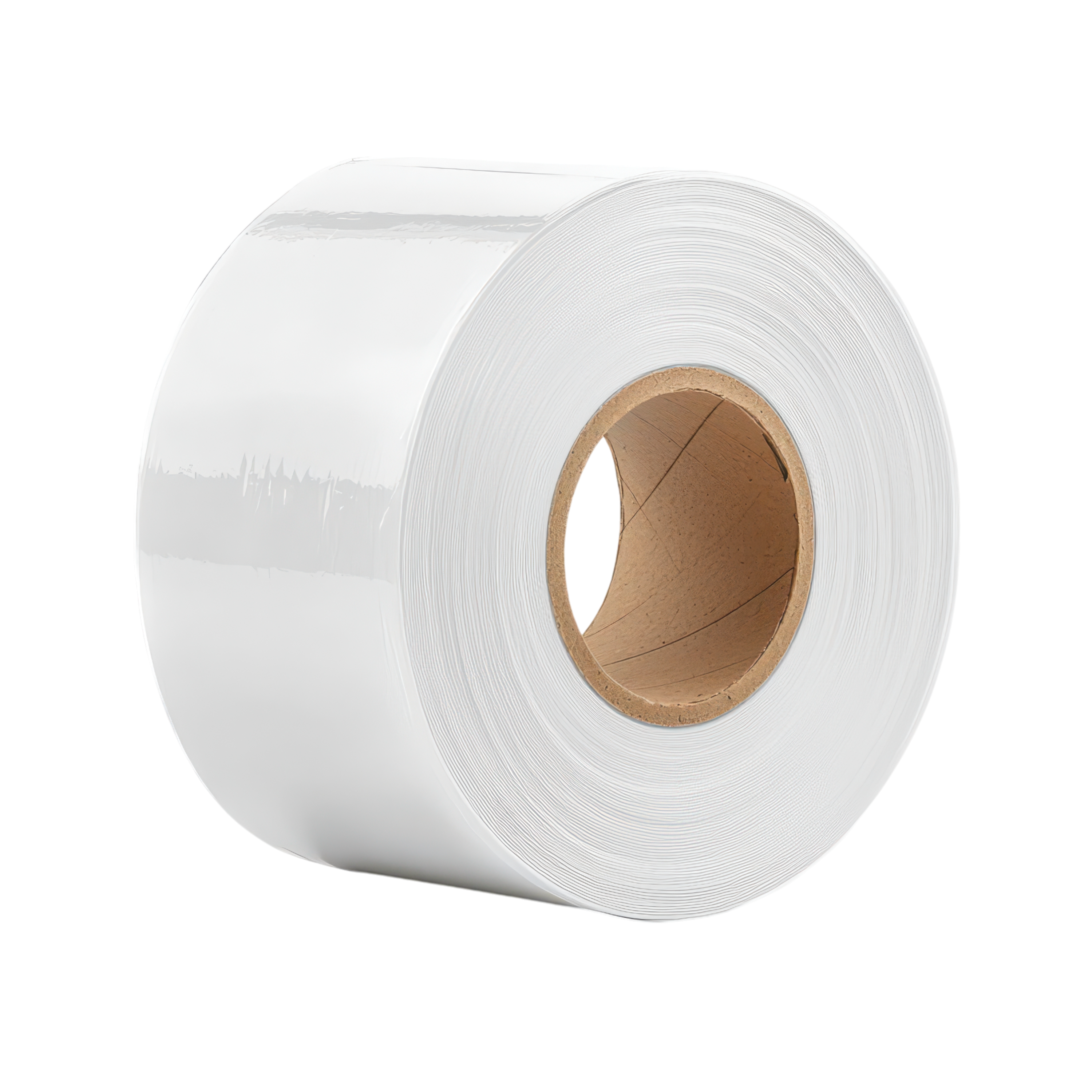
メリット
- 優れたグリップ力
- 簡単な施工
- 汎用的な非粘着性(剥離性)
デメリット
- 機械的強度が低い
- 粉塵が付着しやすい
- 重ね貼りができない
- 非粘着・離型の効果が短期で消失
- 高粘着物質に対しては非粘着が不十分
テフロンテープの特徴とメリット・デメリット
シリコンテープと同じく利用されているのがテフロンテープです。テフロンテープの特徴と、メリット・デメリットは以下のとおりです。
- フッ素樹脂(PTFE)を基材としており、摩擦係数が低い
- 耐薬品性に優れており、ほとんどの化学薬品に侵されない
- 耐熱性・耐寒性に優れており、電気絶縁性が高い
- 水を弾く撥水性に優れている
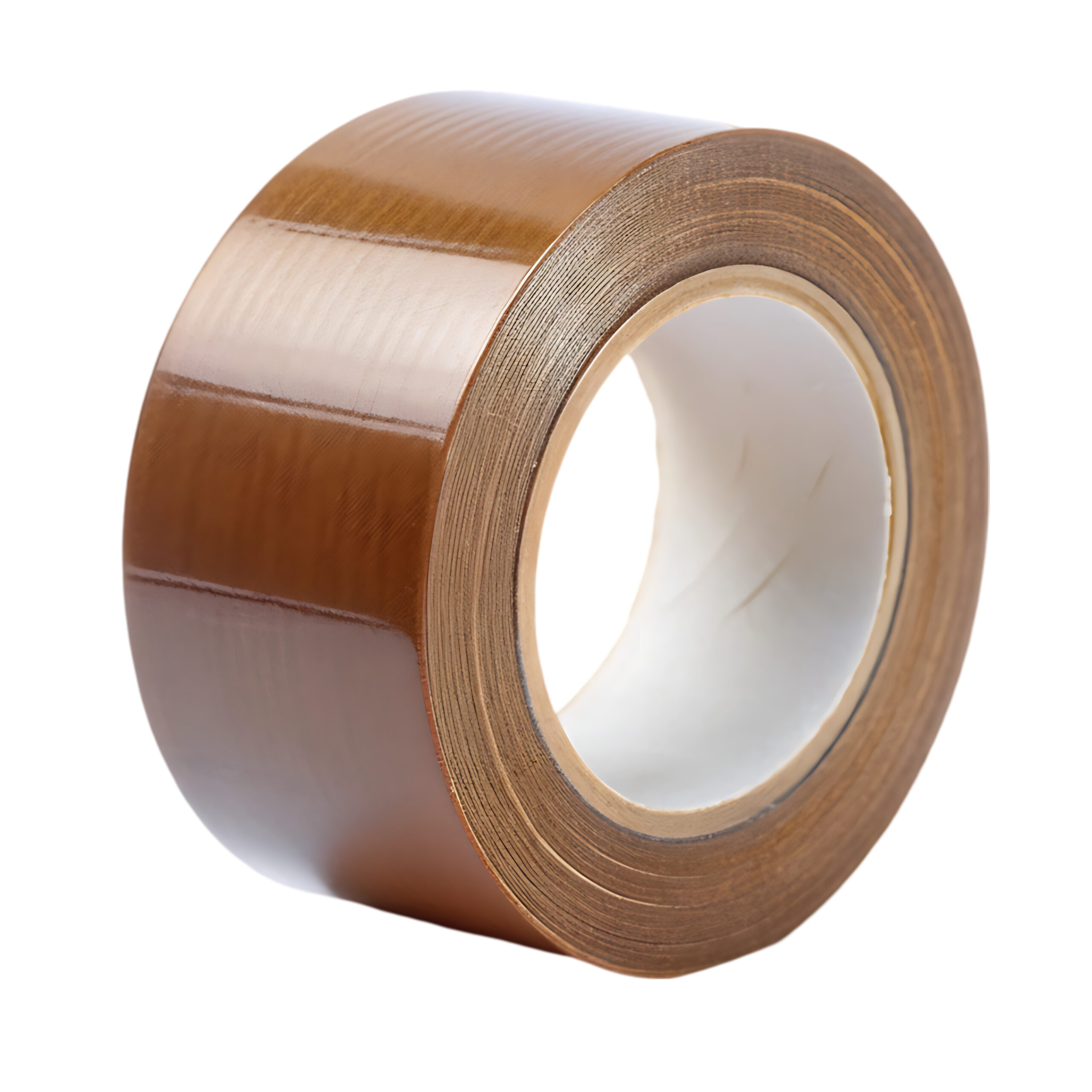
メリット
- 中程度の非粘着性(離型性)
- 優れた滑り性(潤滑性)
- 高い耐熱・耐薬品性
デメリット
- 機械的強度が低い
- 頻繁な交換が必要
- グリップ力がない
- 非粘着・離型の効果が短期で消失
- 高粘着物質に対しては非粘着が不十分
シリコンテープ・テフロンテープによる従来の対策
テープ製造ラインの部品に共通する課題の対策として、シリコンテープ・テフロンテープが使用されています。以下に、各テープごとの従来の対策方法と課題についてまとめます。
テープの種類 | 対策 | 課題 |
---|---|---|
シリコンテープ | ・非粘着性や耐熱性を持つテープを糊が付着しやすい箇所に貼り付ける。 | ・摩擦による劣化や裂けが起きやすい。・粘着剤の種類によっては、表面に付着膜が形成されることがある。 |
テフロンテープ | ・低摩擦性・非粘着性を活かしたテープをテーブル表面などに貼り付けて糊の付着を防ぐ。 | ・素材が柔らかく、長時間の使用で擦り切れやシワが発生しやすい。・定期的な交換が必須で、メンテナンスの手間とコストがかかる。 |
従来テープによる対策は「すぐ導入できる気軽さ」がメリットである一方で、耐久性や完全な剥離性という点は共通の課題です。
シリコン・テフロンテープに代わるプラズマペーパーとは
従来のテープの貼り替えという対策の限界を超える新技術が「プラズマペーパー」です。
プラズマペーパーは、さまざまな母材に非粘着性や離型性を付与する表面処理「プラズマコーティング」をペーパータイプとして使えるように開発した製品です。表面に貼り付けるだけで、手軽に非粘着皮膜を形成できます。鉄やSUS・アルミなどの金属はもちろん、紙やフィルムのような薄い材料にも使用可能。離型性・グリップ力・滑りやすさなど、それらを好きなサイズで貼り付けることもできます。
また、歪まない非粘着処理になりますので、精密機械や僅かな歪みが許されない箇所にも安心してご使用頂けます。
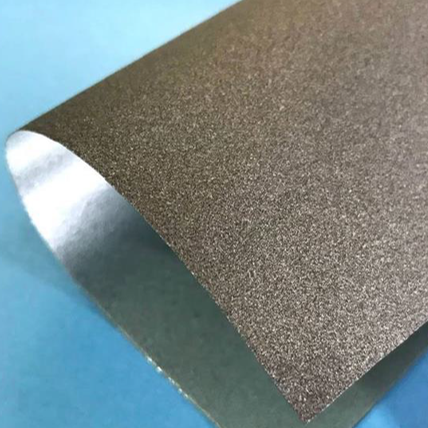
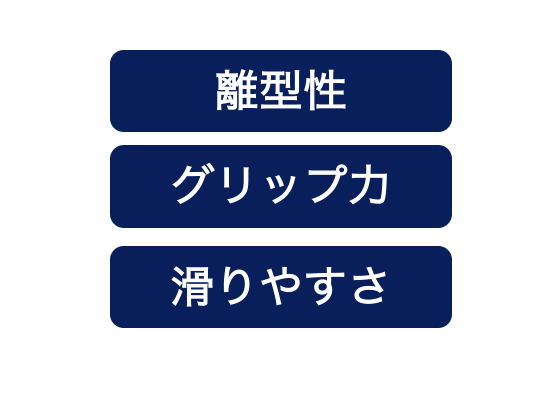
ペーパーを貼り付けるだけで
簡単に機能性を付与できます。
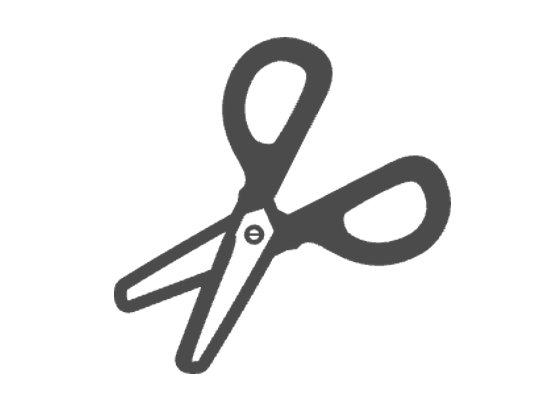
用途別に好きなように切り取って、
必要な箇所に貼り付け可能です。
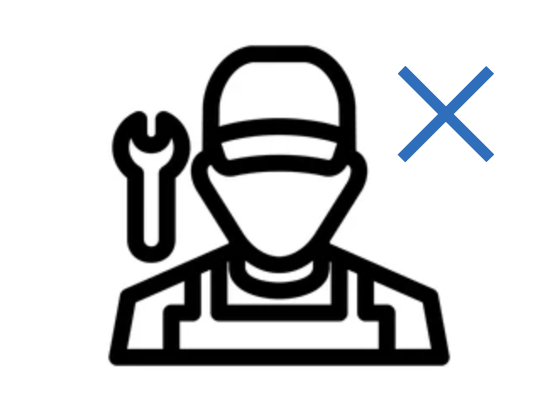
加工対象物にブラストや加熱を
する必要はありません。
プラズマペーパー適用後のメリット
プラズマペーパーを導入すると、以下の3つのメリットが得られます。
- 部品寿命の延長
- 清掃・交換頻度の削減
- 予備在庫管理の負担軽減
高い非粘着性により摩耗や汚れの付着が軽減されるため、交換サイクルが長くなり、日々のメンテナンスにかかる手間と時間を大幅に削減可能です。生産ラインの安定稼働とトータルコストの削減が実現できます。
また、糊の付着が減ることで清掃・交換頻度も削減され、ライン停止時間が短縮されます。部品が長持ちするため交換用の予備在庫を多く抱える必要がなくなり、倉庫コストや発注業務の負担も軽くなる点も大きなメリットです。
プラズマペーパーを適用したある大手企業の成功事例
実際にプラズマペーパーを適用した企業は、以下のような課題を解決し成果を獲得しました。
部品名 | 課題 | 導入後の成果 |
---|---|---|
テープスリッター | ・刃周辺の摩耗・粘着剤付着で連続稼働に支障 | コーティングによる高耐久化で1年以上の耐用年数を実現。 |
テープドロップテーブル&サイド | ・裁断されたテープ表面の糊残り・粉塵が固着し清掃負荷大 | 撥着性により清掃時間を短縮し、ライン停止を大幅削減。 |
トリムガイドドライバー | ・バリ・端材が詰まりやすい・交換サイクルが短い | 2年以上の運用実績。トリミング品質も安定。 |
スプライステーブル&洗浄部 | ・塗布剤の乾燥固着・洗浄不足による不良発生 | 粘着残渣がほぼ付かず、均一な塗布品質を維持。 |
コンベアガイド | ・テープのズレ・貼り付きによるライン停止リスク | コーティングにより安定搬送を実現し、不良数が減少。 |
プラズマペーパーを導入する4つのステップ
プラズマペーパーの効果を最大限に引き出すには、計画的な導入プロセスが不可欠です。弊社では以下の4つのステップをおすすめしています。
- ステップ1:現場の課題洗い出し
- ステップ2:コーティング仕様の選定
- ステップ3:試作・効果検証
- ステップ4:本格導入と運用最適化
各ステップについて順番に見ていきましょう。
ステップ1:現場の課題洗い出し
導入の第一歩は、現場課題の正確な洗い出しです。問題点を特定しなければ、適切な対策が打てず投資効果が無駄になりかねません。まずは「どの部品の摩耗が激しいか」「どの工程の糊残りが生産停止の原因か」を具体的に調査しましょう。
部品の材質や現在の対策状況も記録し、現状を可視化します。この分析に基づき、最も改善効果が高く、投資対効果が見込める箇所から優先的に着手することが重要です。現状把握と優先順位付けが、プロジェクト成功の鍵となります。
ステップ2:コーティング仕様の選定
次に、洗い出した課題に基づき、最適なコーティング仕様を選定します。プラズマペーパーは使用環境や粘着剤の特性によって最適なレシピが異なるため、仕様選定は極めて重要です。
具体的には、使用温度や湿度、接触する薬剤の種類、求める硬度などの条件を基に検討します。現場環境に合わせたカスタマイズが、性能を最大化するうえで不可欠です。
ステップ3:試作・効果検証
仕様決定後は、本格導入の前に必ず試作品で効果検証を行います。実環境で性能を客観的に評価し、導入後の失敗リスクを最小化するためです。テスト部品にコーティングを施し、実際のラインで一定期間運用してみましょう。
清掃性や耐摩耗性、糊残りなどの項目を導入前と比較・評価します。もし期待した効果が得られなければ、仕様の再検討が必要です。事前の試作と効果検証は、投資対効果を見極め、確信を持って本格導入に進むための重要なステップです。
ステップ4:本格導入と運用最適化
試作・効果検証で仕様が確定しましたら、プラズマペーパーを導入いただきます。
プラズマペーパーを使用いただいたうえで、部品交換のタイミングが近づいてきた際には、さらなる長寿命化をはかるべく、部品に直接コーティングを行う「プラズマコーティング」の採用もぜひご検討ください。
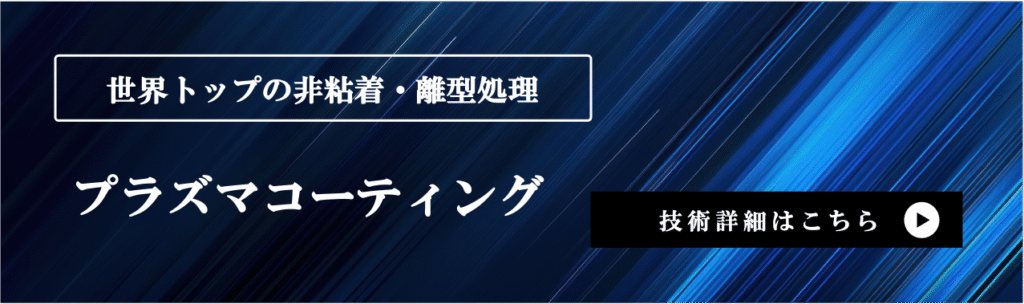
まとめ
本記事では、テープ製造ラインの粘着剤付着や部品摩耗といった課題への対策についてまとめました。従来行われてきたテフロンテープやシリコンテープでの対策は主流であるものの、さまざまな課題がある点にも触れています。
課題を根本から解決する新技術「プラズマペーパー」は、優れた耐摩耗性と剥離性で部品寿命を大幅に延ばし、清掃の手間やライン停止を削減します。成功事例で紹介したように、大手企業でも効果は実証済みです。従来の対症療法から脱却し、生産性向上とコスト削減を実現したい方は、ぜひプラズマペーパーの導入をご検討ください。
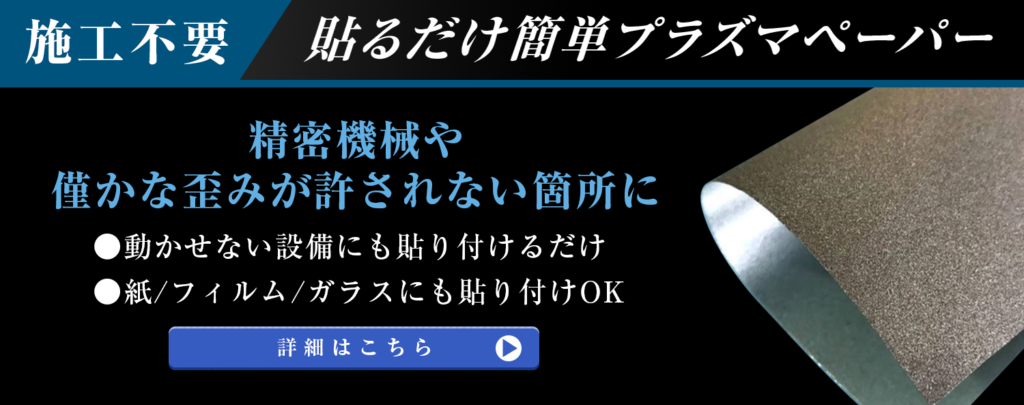
プラズマペーパーの特徴がわかる資料ダウンロード
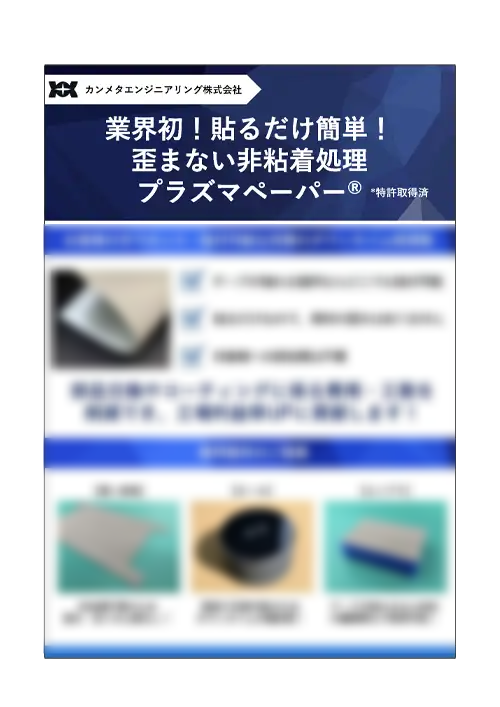